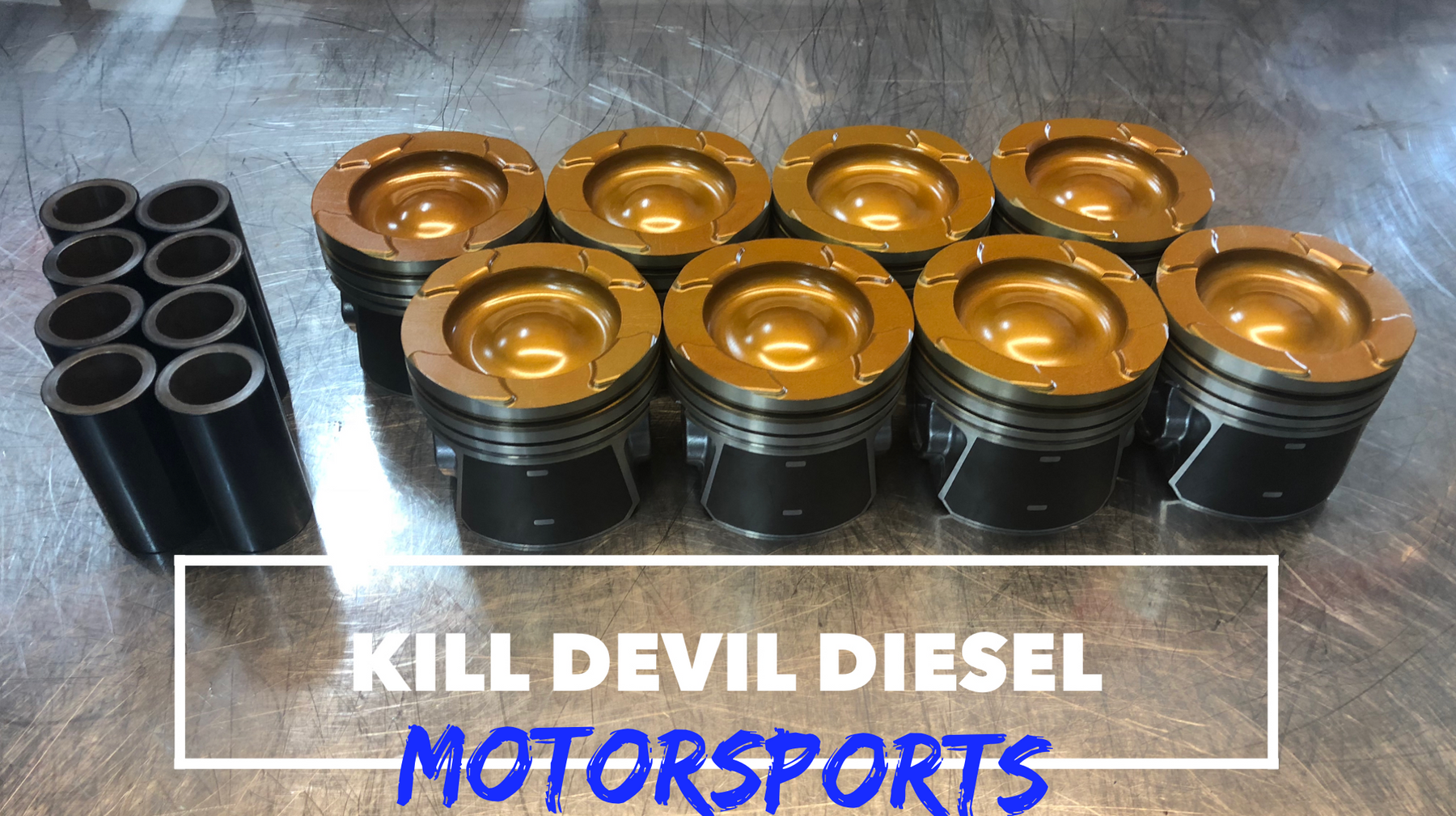
Piston Coatings Explained:
Piston Coatings Explained:
Piston coatings are one of the most common topics we get asked about. In this article we'll discuss the advantages, features and benefits of piston coatings. Not all piston coatings are created equally, we are proud to partner with the industry's most successful piston and coating manufactures to offer superior products to handle the rigors of day to day heavy towing or record setting 1/4 mile passes. There are several different types of coatings, some are designed to be heat barriers, some coatings are designed to be dry film lubricants. We'll also discuss anodizing, a process that changes the surface composition of the aluminum to better protect the base material. Lets break them down -
Heat Barrier Coatings:
Kill Devil Diesel is proud to offer POLYPHEN™ COATING SYSTEM from our partners at TechLine Coating, applied in house, :
Polyphen™ is a resin system used in several coatings including thermal barriers, thermal dispersants and slick release. Polyphen makes use of a unique binding system to retain high temperature stability while reducing thermal transfer. The film thickness as applied ranges from .0005″ to .003″ and is not sensitive to the manner in which it is applied. If a run or other excessive film build occurs it will simply bubble and crack. Polyphen achieves full cure at 300°F, after 1 hour at temperature. When cured, Polyphen is not affected by most chemicals. Polyphen can aid in the more even distribution of heat for a more even surface temperature, helping to eliminate hot spots.
Mahle Ceramic Based Piston Coatings - MAHLE Motorsport now offers a proprietary thermal barrier coating application for any PowerPak performance forged piston – gas or diesel, available through Kill Devil Diesel. This ceramic-based thermal barrier application greatly reduces heat transfer for improved performance and adds a layer of insulation to the piston crown to protect against thermal shock. For added protection and performance, this cutting edge thermal coating is particularly important for use on the crown to prevent hot spots.
While these thermal coatings aren't a guarantee against poor tuning or excessive exhaust gas temps (EGT's), the coatings will broaden the tuning window slightly, and give you more time before meltdown. As with any coating, proper prep and application are absolutely critical to withstand the excessive heat and insane injection pressure found in today's modern Diesel engines. In the event of an injector failure, a faulty nitrous jet, or even simply pulling a long grade with a heavy foot, piston coatings add an extra level of insurance to any build. By focusing more of the heat energy in the combustion chamber, the cooling system absorbs less heat, making the engine more efficient and capturing more of the potential energy out of each droplet of fuel.
Friction Reduction Coatings:
MAHLE Motorsport proprietary Grafal® anti-friction skirt coating is like no other on the market. It is graphite impregnated to reduce drag like many other skirt coatings, but this is where the similarities end. The screen print application provides superior adhesion and is designed to last 100,000+ miles. The unique properties of Grafal® reduce the harsh contact between the piston skirt and cylinder bore, resulting in much less wear on the bore and significantly reduced piston skirt fatigue.
All 6.0 and 6.4 and 6.7 Powerstroke, as well as many Duramax and Cummins pistons come with this Grafal coating from the factory, and it is not uncommon to disassemble engines with over 250k miles on them with the skirt coating in remarkable shape.
Anodizing:
Anodizing is an electrochemical process that converts the metal surface into a decorative, durable, corrosion-resistant, anodic oxide finish. Aluminum is ideally suited to anodizing, although other nonferrous metals, such as magnesium and titanium, also can be anodized.
The anodic oxide structure originates from the aluminum substrate and is composed entirely of aluminum oxide. This aluminum oxide is not applied to the surface like paint or plating, but is fully integrated with the underlying aluminum substrate, so it cannot chip or peel. It has a highly ordered, porous structure that allows for secondary processes such as coloring and sealing.
Anodizing is accomplished by immersing the aluminum into an acid electrolyte bath and passing an electric current through the medium. A cathode is mounted to the inside of the anodizing tank; the aluminum acts as an anode, so that oxygen ions are released from the electrolyte to combine with the aluminum atoms at the surface of the part being anodized. Anodizing is, therefore, a matter of highly controlled oxidation the enhancement of a naturally occurring phenomenon. Source - Anodizing.com.
Practical use application, anodizing drastically improves the hardness and "toughness" of aluminum, and is commonly used in the ring grooves of forged pistons to combat excessive ring groove wear in extreme applications. Most factory diesel pistons are cast aluminum, but come with a steel ring carrier casted into the piston to help with ring wear. In a demanding racing application where a stronger forged piston must be used and a steel ring groove is unavailable, anodizing the ring groove has been proven to improve piston life by more than 5 times.
Some manufacturers like CP/Carillo opt to hard coat anodize the entire piston to help tolerate the incredibly high injection pressures of modern diesels. Anodizing the piston reduces wear and material transfer. Anodizing can be done to the entire piston or a selective area depending on its usage. Anodizing the entire piston has been shown to be very durable in demanding applications like drag racing and sled pulling.
The Application Process:
In order to properly apply the piston crown coating, first pistons are cleaned with solvent/acetone to eliminate surface contamination. Next, the regions of the piston that we don't want to apply the coating to are shielded and masked off to expose only the crown of the piston. Next the pistons are abraded with 400 grit aluminum oxide to give the finely machined surface finish enough texture for the coating to adhere. Following the abrasion process, the pistons are again chemically cleaned to be sure they are completely free of contamination, then allowed to air dry to remove any residue. The pistons are again masked off to expose only the piston crown, to eliminate coating the sides/ring grooves of the piston. Next, the pistons coating is applied, via professional HVLP painting gun, in multiple light coats to ensure even coverage without runs or drips. After allowing to air dry for a short period, the pistons are again unmasked, then baked in our industrial convection oven at 422 degrees Kelvin (300*F) for one hour, then allowed to cool slowly to room temperature. The new coating is now 100% cured and ready for service!!
Piston coating summary -
While engines ran for the last 100 years without coatings of any type, modern technology has drastically improved the science of piston coatings. While the piston appears to be a relatively simple, stable, solid component on the surface, during operation the piston expands and flexes under combustion temperature and pressure. This movement and stress in the piston absolutely requires 100% roper piston prep to avoid delimitating the coating. Many racers have been using piston coatings for decades, but as the benefits of piston coatings have proven themselves throughout the years, manufacturers like Ford and GM adopted this technology. Many OEM's have used skirt coatings since the early 2000's because of the undeniable efficacy in modern diesel engines. When it's in the budget we highly recommend adding protection and durability to your next KDD piston order!!
Resources:
For more great piston tech, please take a look at this video from Mahle, where our buddy Eric is interviewed about piston coatings:
Check out this great video from Mahle Here!!
For an even deeper dive into the world of coatings, check out this article from our friends at Engine Builder Magazine where they discuss more piston coating tech.
JE Pistons also has a great article on piston anodizing, click here!
And here's a great video discussing piston compression ratio calculation from Mahle as well.