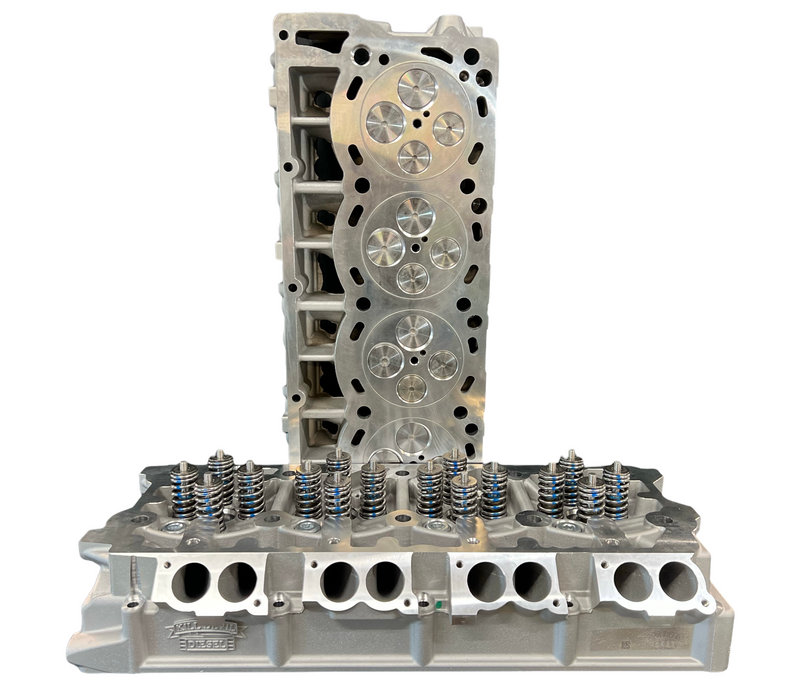
ICON Series Aluminum 0-Ringed 6.4 Cylinder Heads - Street Port
SKU: 64P-CH-572-2
- Refundable Core Charge: "Cores" are used parts that can be used in re-manufacture. The Refundable Core Charge is added to your order and when you send your “core” in, we assess the value and will refund up to the Refundable Core Charge amount. +
- Regular Price Plus Core: $3,499.00 USD
Aluminum O-Ringed Cylinder Heads
Features & Details:
- Lead Time Applies - Call For More Details
- USA MADE
- Designed to handle the rigors of heavy-duty daily use
- 24% better airflow than stock heads
- 82% better cylinder swirl than ported factory-style heads
- Hardened seats and heavy duty guides for unmatched durability
- Improved dual layer water jacket eliminates hot spots
- Reinforcements/Gussets to distribute head stud clamping load
- Manufactured on state-of-the-art, tool-steel, permanent mold tooling
- O-ringed to prevent head gasket failure
- Modern high velocity swirl port technology similar to 6.7 Powerstroke
- Aluminum construction offers superior heat dissipation for added longevity
- Weight savings of 75+ lbs lighter than factory heads
- Made in the USA (yeah, we already said that, but it's worth saying twice!) From start to finish, designed, casted, machined in the USA, and assembled by hand, right here in North Carolina
- ICON Series VIDEO
- ICON Series Install Notes
Description:
Extended Lead Time Applies
KDD ICON Series Street Port Cylinder Heads offer superior performance to anything else on the market - using state of the art casting technologies we molded the ports to improve airflow and cylinder swirl beyond what is possible within the limitations of factory style castings. The ICON series was a ground up, clean sheet design featuring "as-cast" intake and exhaust ports that outperform CNC ported factory style heads, thicker deck surface, dual layer water jacket with reinforced gussets to better distribute head stud clamping load, hardened seats and guides for superior wear characteristics over the long haul, and best of all, the ONLY USA Made aftermarket head available for the 6.0 and 6.4 Powerstroke.
Porting the factory heads, or aftermarket replacement style heads has always been a trade off: increase flow but sacrifice swirl. "Swirl" is the preferred mixture motion of a direct injected diesel engine (opposed to "Tumble" which is preferred in other applications). Ideally the injector should act like a centrifuge, where each fuel vapor droplet is sprayed across bands of swirling air...if each vapor droplet doesn’t continue to find fresh oxygen before the fuel is burned completely, the left over fuel comes out of the exhaust pipe as soot. If that fuel had been burned in cylinder, the engine would have produced more power, with lower EGT, and better turbo spool up and throttle response. That was the goal of the ICON Series heads, maximize flow without killing swirl for optimal fuel mixture...to actually burn all of the fuel that's injected. We performed extensive CFD (computer fluid dynamic) analysis to determine the best design for port development, to not only maximize airflow, but the cylinder swirl conditions as well. Powerstroke 6.0 and 6.4 engines came from the factory with what is now considered "dated" "Low Velocity Swirl Ports" which use restrictions in the port to push the air to the outside of the cylinder walls to improve swirl, the 7.3 and the 12v Cummins also used similar shaped ports, with a bias (read: blockage) in the port to direct the air to one side of the port, which only uses half of the port. This is effective at low valve lift...however the first thing everyone does when porting the factory style heads (that is to mean ANY other head on the market, factory, stock replacement style) is to grind the restrictions out of the head - which brings the flow numbers up on a flow bench, but destroys the "mixture motion" sacrificing swirl for tumble.
We use our Superflow SF1020 flow bench nearly every day for testing and development, while it's proven to be an invaluable tool, a flow bench is a fairly one dimensional tool to evaluate certain port characteristics - it doesn’t tell the whole story. A flow bench measures airflow across the valve in a static environment, the valve is opened a specified amount, the rate of airflow is recorded (in CFM, cubic feet per minute)...the valve is opened further, the airflow is recorded, etc, this is how a flow chart is produced. This provides great information (by the way, we typically look at low and mid lift airflow first, and worry about airflow at peak valve lift last, as the valve spends more time through low and mid-lift ranges and less time at peak lift). Never the less, one of the most common questions we get is "How much do they flow?", where presumably the customer is looking to compare one simple number to other advertised numbers on the market...while it only paints a one dimensional portrait of the operating dynamic, factory heads flow about 160cfm at peak valve lift, our ICON heads flow over 200cfm, but more on that later. While this is valuable information, it is not 100% representative of the true operating dynamic of a running engine, where the pressure, temperature, and RPM changes, and the valves open and close dozens of times per second. For that, we employed "CFD Testing", or "computer fluid dynamics" to gain a more accurate picture of how things work in a running engine. To date we have never seen this level of engineering and design used in ANY aftermarket diesel cylinder head, this level of technology is typically used by the original equipment manufacturers.
During the ICON development, we set up our CFD testing criteria thusly: 60 psi intake manifold pressure, 150 degree F intake air temp, 4,000 RPM, using our S2 Camshaft valve opening and closing events to measure the movement and volume/mass of the air entering the cylinder each cycle - That's right...we actually measured the air mass, in cylinder, comparing stock heads, ported stock heads, competitors heads, and our new ICON series heads. We wanted to actually evaluate for perhaps the first time ever in the diesel performance industry what the port and cylinder airflow dynamic is like in a running engine. The results are pretty amazing. OE manufacturers like Ford and GM no doubt use similar CFD testing, but at low boost to develop the efficiency range of the engine, optimized around low boost and emissions. We’re unaware of anyone else in the diesel performance world who has taken this kind of engineering approach to developing a performance cylinder head.
Our testing confirmed a few things we suspected: our previous best flowing heads (iron CNC ported 6.4 heads, 217 cfm on a flow bench) increased total ‘in cylinder’ air mass by a respectable 5.1%, but it also confirmed our suspicions that it significantly diminished cylinder swirl. All of the fuel in the world is no good if it can’t mix with air. This is where the limitations of the factory style geometry became readily apparent. The surrounding water jackets, pushrod locations, and overall design and shape of the factory-style head castings mean that options are extremely limited in where material can be safely removed to increase flow, and by doing so swirl is inevitably negatively impacted. On the ICON Series heads, we engineered the optimal port FIRST, then built the water jackets around it, so we are not only able to match the airflow of ported iron heads, but also able to utilize modern "high velocity swirl port" technology (used in 24v Cummins, Duramax, and 6.7 Ford).
By totally changing the port geometry (and re-engineering the surrounding water jackets and adding massive structural reinforcements, we were able to drastically increase both mass flow, and swirl. The heads will still accept conventional intake and exhaust manifolds - the port locations are the same, but the path the air takes from the intake flange to the valve and from the exhaust valve to the exhaust port flange is drastically improved over factory heads, and over CNC ported factory style heads.
We’ve added some pictures of our development and test results below, you can see in the color gradient how much swirl is improved in the new heads vs the old, as well as the drastic difference in all of the extra structural rigidity we’ve added to the casting (dual layer water jackets, gusseted/trussed head bolt reinforcements, extra ribbing and webbing in critical areas to disperse clamping load over a greater area, 25% thicker deck surface, etc). The new ‘as casted’ Street Port ICON heads already outflow everything available, with far better cylinder filling as seem by our charts, with optimized mixture motion to help all of that air burn the fuel completely. The Street Port heads add an additional 7% air mass in cylinder while also improving on the swirl dynamics. (For truly next level performance, we recommend our CNC "Race Port" ICON heads with larger valves, for a massive 22% increase in air mass, 240+ CFM - lead time applies).
We are in the early stages of obtaining our 50 state EO number for this product through CARB and SEMA. We also have ample testing data from 5 gas analyzer during chassis dyno testing, combined with real world smog test results to suggest that these cylinder heads not only pass, but improve the emissions over the factory heads.
Please call or email with any questions, 252-725-1222 or sales@killdevildiesel.com
This listing is for a pair of cylinder heads, hand assembled, with USA made valves and springs.